News
Increasing Life of Artificial Muscle up to 100 times
─Aiming towards Application to Body-Mounted Assistive Devices─
Updated in March 2020
New Energy and Industrial Technology Development Organization (NEDO) is working on “Developing Next-Generation Artificial Intelligence and Robot Core Technology.” Recently NEDO and Chuo University Nakamura Laboratory (Science and Engineering Department) succeeded in extending the life of artificial muscle up to 100 times by utilizing the stretch crystallization property of rubber. This property can prevent cracks from expanding in the artificial muscle.
Axial fiber-reinforced artificial muscles have superior contractile properties compared to general artificial muscles which had shorter life.
In the future, the team aims to apply this result to new models of Airsist series─variable viscoelastic orthoses (braces) that can assist lower limb movements.
Chuo University exhibited the axial fiber-reinforced artificial muscle and Airsist at the International Robot Exhibition 2019 (iREX2019) held at Tokyo Big Sight (Tokyo International Exhibition Center) during December 18-21, 2019.
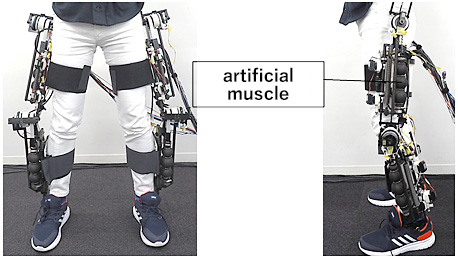
1.Overview
In our aging society, labor shortage is a major issue and work efficiency is being improved by automation and mechanization. However, in fields like agriculture, manufacturing and nursing care, there are tasks that are difficult to automate and mechanize due to work efficiency or lack of space. For this reason, practical implementation of body-mounted assisting devices that reduce workload can help us.
One of the driving devices (actuators) used in the body-worn assisting device is the axial fiber-reinforced artificial muscle, a type of artificial muscle made from pneumatic rubber. Reinforcing fibers are aligned in an axial direction and inserted into a rubber tube to constitute the artificial muscle. By applying air pressure to this, it expands radially and contracts axially, allowing it to be used as an actuator (Fig. 2). In addition, this artificial muscle is lightweight, flexible, and has excellent contraction characteristics compared to conventional McKibben type artificial muscles.1 It contracts up to 38% or more when driven at low pressure. Its disadvantage, however, is the great deformation of rubber. Cracks are likely to occur due to rubber deterioration and product life is short.
This time, NEDO and Chuo University Nakamura Laboratory have utilized the extensional crystallization properties of rubber in the axial fiber-reinforced artificial muscles to prevent expansion of cracks. As a result of this, the team was able to extend the life of artificial muscle up to 100 times. In the future, the team shall apply this result to variable viscoelastic orthosis (brace) to assist lower limbs.
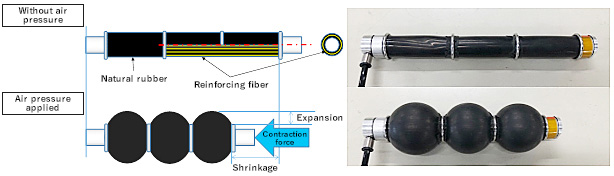
2.Achievements
Figure 3 below shows a model for extending rubber life of rubber based on the extensional crystallization characteristics. When rubber is strained from external stress, the weakest bond in the rubber molecular chain can get cut when the stress reaches up to a certain level. Consequently, a heavy load is applied to the adjacent molecular chain that has been cut, and the same can happen to the next molecular chain. When this is repeated, the crack can spread and eventually break. By utilizing the extensional crystallization properties of rubber, however, the crystal layer formed by extension can prevent cracks from spreading and can extend the life of the rubber material.
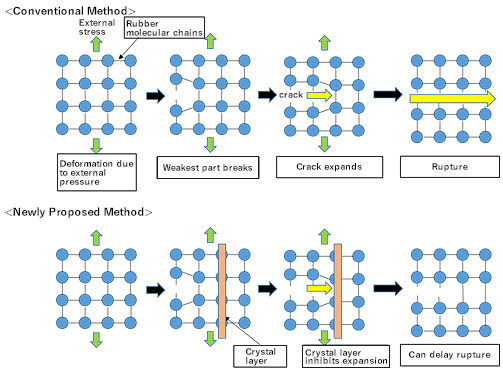
Fig. 4 shows the measurement results of the crystal layer by wide-angle X-ray diffraction3 (top) and the stress-strain curve of natural rubber (bottom). The horizontal axis of the stress-strain curve shows strain, and the vertical axis shows stress. The rubber is stretched 7 times its original length and shrunk back to its original length (blue triangles indicate the direction of stretching and shrinking). When the rubber’s length reached 4 times the original length, a bright spot indicating the formation of a crystalline layer is observed in the wide-angle X-ray diffraction measurement. And when shrinking, the bright spot can be observed before the rubber length is restored to 3 times the original length. The above results indicate that the extension crystallization property is a reversible reaction. In order to maintain the crystal layer, it need to be used within the range shown by the red line.
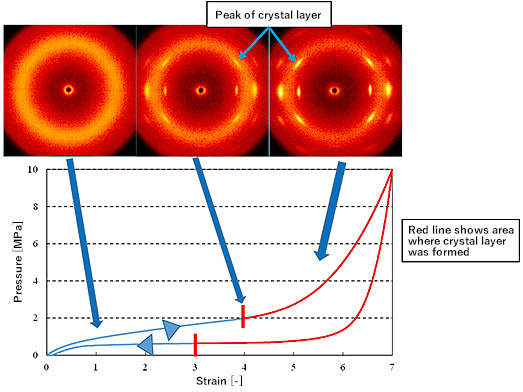
Based on this finding, the team controlled the artificial muscle to keep the rubber stretched to a certain extent in order to maintain the crystal layer of the rubber. Until now, it broke when the number of stretching/shrinking reached several hundred to several thousand times, but when the team used the newly developed artificial muscle control method, it can be stretched more than 800,000 times. Thus, the initial target value of this research─200,000 times─was successfully achieved. Assuming that the wearer is assisted about twice a minute, the device can be used 5 hours/day for about a year. (Fig. 5).
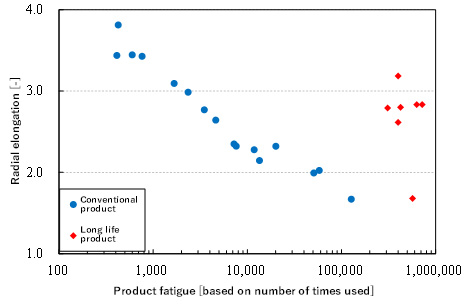
By applying this artificial muscle to body-worn assisting devices, there are four advantages:
1) Light weight and high output allow high mobility of the drive unit and enable miniaturization. Also, compared to McKibben type artificial muscle, the same output can be obtained at low pressure, so that air pressure sources like compressors can be downsized.
2) It has a flexible structure. Rigid control is possible through open loop (control mechanism without sensor feedback; features simple sensor-less structure and control law). In addition, it has superior back drivability (property of transmitting the force received on the actuator’s output side to the input side) compared to motors with reducers and is inherently safer.
3) Because this artificial muscle has more freedom of shape, it can be applied to devices of different structures.
4) Requires small number of parts and the cost of raw materials is low.
3.Future plans
NEDO and Chuo University will apply these results to the new Airsist series of variable viscoelastic braces to assist lower limbs, as well as to NEDO's other projects like excavation work in extreme environments (e.g. deep seabed and the moon). The team is now studying to apply this research to a peristaltic pump for transporting earth and sand, which is expected to display high performance. Furthermore, the team aims to commercialize Airsist through SoLARIS Inc., a venture company from Chuo University.